Overview
Rapid prototyping significantly accelerates new product development. Imagine transforming ideas into tangible products within days using advanced manufacturing processes.
From 3D printing, Sheet Metal Fabrication and CNC machining for plastics and metals, diverse methods are employed. The turnaround is astonishingly quick, thanks to these rapid prototyping techniques.
Various surface finishes ensure prototypes achieve optimal functionality and aesthetics. These finishes can enhance the durability, appearance, and performance of the final product. Techniques such as polishing, painting, anodizing, and plating are employed to attain the desired surface quality. Selecting the appropriate surface finish is crucial for meeting the specific requirements of the application, whether it involves reducing friction, improving corrosion resistance, or achieving a particular visual appeal.
The Role of Rapid Prototyping
Rapid prototyping helps bridge the gap between conceptual drawings and market-ready products. It’s a critical phase in new product development.
By leveraging rapid prototyping techniques like 3D printing, CNC machining, Sheet Metal Fabrication, engineers can iterate on designs swiftly. Iterations informed by physical prototypes facilitate better decision-making, minimizing costly errors.
Terms like “on-demand manufacturing” and “contract manufacturing” align closely with the principles of rapid prototyping.
Benefits for Innovation
Rapid prototyping is pivotal for fostering innovation, enabling swift ideation and creation. This accelerates the cycle from concept to tangible product, facilitating quicker market entry.
The iterative approach allows for continuous improvement, with real-time feedback incorporated at each stage. This minimizes risks and enhances the functionality of the final product.
Speed to market is crucial for staying ahead in competitive industries.
Material versatility: Engineers can experiment with various materials—plastics, metals, sheet metal—crafted through CNC machining and 3D printing, ensuring a robust vetting process for optimal material selection. This agility ensures that the end product meets high performance and aesthetic standards.
Accelerating Time to Market
Utilizing rapid prototyping can significantly shorten the product development lifecycle, allowing for faster entry into the market.
Rapid prototyping mitigates risks and enhances product functionality by incorporating real-time feedback.
This approach enables engineers to experiment with various materials, ensuring the final product meets high performance and aesthetic standards.
Key Manufacturing Processes
3D Printing leverages additive manufacturing to create intricate geometries that traditional methods can’t achieve. It enables rapid prototyping, producing parts layer-by-layer from digital 3D CAD models.
CNC Machining uses subtractive processes to shape both plastics and metals with remarkable precision. It’s ideal for creating functional prototypes that meet final product specifications, ensuring robustness.
Sheet Metal Fabrication involves cutting and bending metals into complex shapes. This process is crucial for sheet metal prototypes requiring structural integrity and durability.
3D Printing prototypes
These advantages make 3D printing a preferred choice for initial iterations in product development.
By leveraging additive manufacturing, you can swiftly test form, fit, and function.
This accelerates the path from concept to market, minimizing risk and improving product quality.
CNC Machining prototypes
CNC machining delivers unparalleled precision and versatility, crucial for high-fidelity prototypes.
Since its inception, CNC machining has revolutionized the manufacturing industry by enabling the rapid production of functional prototypes. These prototypes not only reflect the design but also assist in evaluating the mechanical properties of the final product.
Utilizing CNC machining, engineers can work with a wide range of materials, including metals and plastics. This flexibility allows for the creation of prototypes that can withstand rigorous testing, optimizing the design process significantly.
Moreover, the high repeatability and tight tolerances offered by CNC machining ensure that each prototype is consistent with the original design. This is vital for quality control and for making iterative improvements to the prototype.
Ultimately, CNC machining is indispensable in new product development for its ability to produce precise, durable, and functional prototypes swiftly.
Sheet Metal Fabrication prototypes
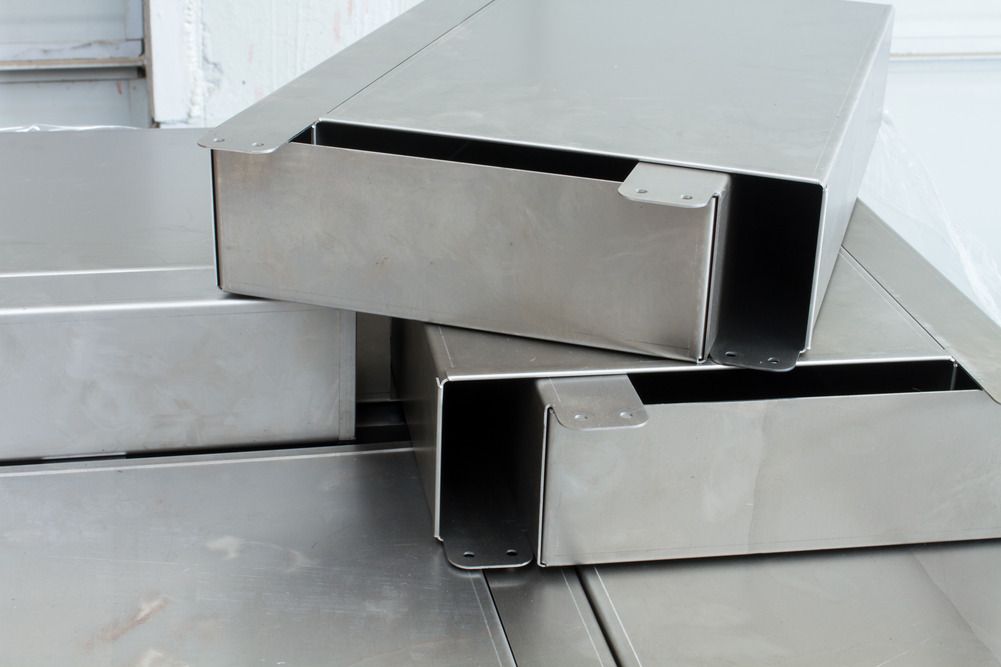
Sheet metal prototypes are indispensable for precise applications.
Utilizing sheet metal fabrication accelerates the prototyping process. This method allows for rapid development of custom sheet metal components, making it possible to test functionality and fit within days. Importantly, materials like aluminum, steel, and copper, etc. can be utilized to match end-use requirements, ensuring a high degree of accuracy.
These sheet metal prototypes also provide robust mechanical properties.
Sheet metal fabrication processes such as laser cutting, hydraulic press bending, and punching are scalable – from a single prototype to mass production – ensuring seamless transitions from prototype to production. This makes it an ideal solution for industries requiring quick and efficient prototyping.
Material Selection
Choosing the right material is a critical first step in rapid prototyping.
It involves understanding the specific requirements (e.g., strength, flexibility) to ensure the selected material meets functional and performance criteria. Materials like plastics and metals each offer distinct advantages depending on the application.
Terms like “thermoplastics” and “stainless steel” are commonly mentioned to highlight their respective properties.
Plastic vs. Metal Prototypes
When selecting materials for rapid prototyping, it’s imperative to balance cost, durability, and the functional requirements of the new product development process. Both plastic and metal prototypes play pivotal roles, addressing specific needs effectively.
Plastic prototypes are excellent for early-stage design validation. They allow for quick iterations.
Conversely, metal prototypes are favored for their superior strength and durability, suitable for stress testing.
Consider CNC machining for plastics when speed and flexibility in design changes are crucial.
Meanwhile, CNC machining for metals is ideal for prototypes needing high precision and mechanical stress.
Ultimately, the choice between plastic and metal hinges on project goals. Proper material selection ensures successful prototype performance aligned with end-use requirements.
Surface Finishes and Treatments
Surface finishes and treatments are essential aspects of the prototyping and manufacturing process. They enhance the functionality and aesthetic appeal of the final product.
Advancements in surface finishing technologies have expanded possibilities. Options such as anodizing, powder coating, and electroplating offer varied benefits for different materials, enhancing both appearance and performance.
For instance, anodizing not only increases corrosion resistance but also allows for color customization on metal parts. Powder coating provides a durable, uniform finish, unparalleled by traditional paint applications. Electroplating, on the other hand, applies a thin metal layer to improve wear resistance and reduce friction.
These finishing processes ensure that the prototypes not only meet the required specifications but also exceed them. They play an important role in industries ranging from aerospace to consumer electronics, where the smallest detail can make a significant impact.
Understanding and choosing the right surface finish or treatment is crucial for product success. It can significantly enhance durability, functionality, and market appeal.
On-Demand Manufacturing
On-demand manufacturing redefines traditional production, allowing for unprecedented flexibility and efficiency. By enabling rapid response to market needs, companies can manufacture parts and products only when required, minimizing inventory and reducing warehousing costs.
This approach leverages cutting-edge rapid prototyping techniques like 3D printing, CNC machining for plastics and metals, and sheet metal fabrication. It streamlines the production process, ensuring high-quality and precision-managed outputs within short timeframes. As a result, businesses can swiftly adapt to changing market demands and accelerate new product development cycles.
Flexibility and Scalability
Rapid prototyping offers unmatched flexibility and scalability in new product development, enabling efficient transitions from concept to reality.
- Adaptability: Tailor designs and production methods swiftly.
- Speed: Produce prototypes in days rather than weeks.
- Cost-Efficiency: Mitigate initial investment risks with on-demand manufacturing.
- Customization: Easily modify and iterate designs.
- Volume Scaling: Ramp up production seamlessly as demand grows.
These capabilities ensure that businesses remain competitive and responsive to market fluctuations.
Moreover, on-demand manufacturing supports sustainable practices by reducing waste and minimizing excess inventory.
Cost Efficiency
Rapid prototyping is a game-changer when it comes to cost efficiency in new product development. By leveraging technologies like 3D printing and CNC machining, businesses can significantly reduce upfront tooling costs.
Transitioning from traditional methods to rapid prototyping minimizes initial financial risks.
Furthermore, rapid prototyping allows for quicker iteration cycles, drastically reducing the time and money spent on costly reworks and adjustments. This agile approach enables companies to perfect their designs without substantial financial burdens.
Finally, the inherent flexibility of on-demand manufacturing facilitates just-in-time production, which optimizes resource allocation and minimizes inventory costs. In essence, rapid prototyping empowers businesses to maintain fiscal prudence while driving innovation forward.
TABLE OF CONTENTS
Let’s Kickstart Your Custom Manufacturing
Please send your inquiries to the above email and provide as much detailed information as possible in your inquiry, e.g. 3D CAD models, 2D engineering drawings(which should detail materials, tolerances, surface finishing requirements, etc.), artwork files, and quantities needed.