Overview
When the design team at a burgeoning tech startup encountered repeated delays due to extensive prototyping phases, they knew something had to change. That’s where SLA 3D printing entered the picture. SLA is transformative. By leveraging stereolithography (SLA) printing, rapid prototyping underwent a significant evolution. Designers now produce complex prototypes in a fraction of the time.
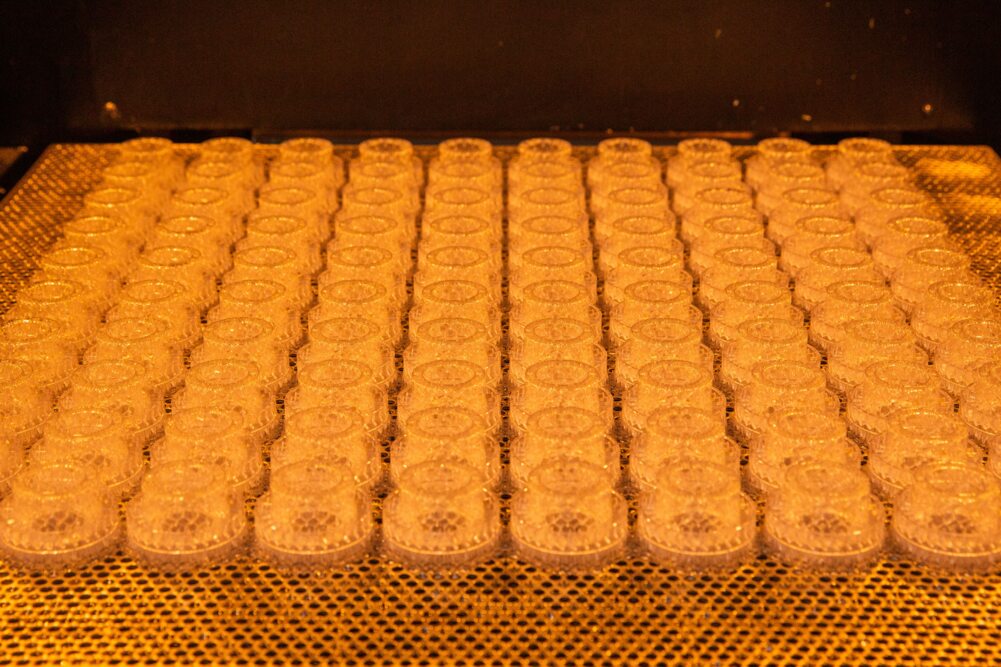
Speed and Efficiency
SLA printing’s unparalleled speed dramatically shortens design cycles, a crucial factor in competitive industries. Companies can iterate more rapidly, refining their prototypes with each iteration without the previously associated time delays.
This acceleration not only saves time but also reduces costs, leading to “time-to-market” advantages. By minimizing the turnaround for each prototype, organizations can devote more energy to innovation. In this way, the faster production cycle afforded by SLA printing transforms how businesses approach product development.
Accelerating Design Iterations
SLA printing accelerates design iterations, a critical advantage in product development, by drastically reducing prototype production times. Rapid prototyping enables designers to refine concepts swiftly and efficiently.
Given shorter production cycles, teams can implement feedback quicker. This fosters a “fail fast, learn fast” environment, crucial for innovation. Accelerated iterations minimize downtime, enhancing productivity.
Rapid iteration boosts product innovation by reducing development time.
Ultimately, SLA printing allows organizations to validate designs faster and more frequently, enhancing the overall quality and performance of the final product. By cutting down lead times and streamlining the prototyping process, SLA printing is key to staying competitive in fast-paced markets.
Rapid Turnaround Times
In the realm of rapid prototyping, swift turnaround times are paramount for maintaining a competitive edge.
- Accelerated production cycles: SLA printing can produce complex parts within hours.
- Efficient design adjustments: Immediate feedback implementation is feasible, enhancing innovation.
- Reduced downtime: Quick iterations mean less waiting and more doing.
- Enhanced productivity: Teams can work on multiple prototypes simultaneously.
These factors collectively contribute to a rapid development process, enabling faster market entry.
By minimizing lead times, businesses can allocate more resources to refining and perfecting their products.
This agility allows companies to stay ahead in industries that demand constant innovation and quick adaptation.
Precision and Quality
SLA printing excels in delivering high-resolution prototypes with micron-level accuracy, ensuring that even the most intricate details are preserved, a feat further advanced by 3D printing techniques.
With its exceptional precision, this additive manufacturing technology surpasses traditional prototyping methods, allowing for the production of parts that closely mirror the final product’s specifications.
The terms “high-resolution” and “fine-detail” are commonly associated with SLA printing due to its ability to achieve sub-millimeter accuracy.
High-Resolution Outputs
Stereolithography (SLA) printing is celebrated for its high-resolution outputs.
This advanced technique leverages ultraviolet (UV) lasers to cure photopolymer resins, creating finely detailed prototypes with remarkable precision. The laser’s ability to target specific points in the resin layer by layer allows for incredibly smooth surfaces and intricate geometries that other methods struggle to achieve. This ensures that prototypes are not only visually accurate but also functional in mechanical testing.
Moreover, each layer can be as thin as 25 microns, yielding parts with superior surface finish. This degree of resolution is particularly beneficial for industries such as aerospace, medical devices, and consumer electronics, where fine detail and precision are paramount. The capability to produce such high-quality outputs makes SLA an indispensable tool in the prototyping phase.
Businesses gain competitive advantages by utilizing SLA’s high-resolution capabilities to validate design concepts early. This enables rapid identification and correction of flaws before mass production, thereby reducing time to market and associated costs. The precision delivered by SLA printing translates to higher fidelity in the final product, fostering confidence in the design’s viability and performance.
Complex Geometries
SLA printing enables the formation of highly intricate and complex geometries with outstanding precision.
In recent years, advancements in SLA technology have revolutionized the creation of detailed prototypes, surpassing traditional manufacturing methods in complexity and accuracy.
The ability to produce interlocking and nested parts without the need for assembly greatly enhances design possibilities in engineering and product development.
Moreover, due to its finely-tuned layering process, SLA can achieve smooth surfaces with high resolution, essential for parts with elaborate geometries, from intricate meshes to organic shapes.
This capability enables engineers to push boundaries and create prototypes that were once thought impossible.
Smooth Surface Finishes
SLA (Stereolithography) printing excels in delivering exceptionally smooth surface finishes, a critical factor in high-fidelity prototyping.
- High Resolution: SLA can achieve layer thicknesses as thin as 25 microns, resulting in remarkably smooth surfaces.
- Minimal Post-Processing: The superior smoothness of SLA-printed parts reduces the need for extensive sanding or finishing.
- Precision Details: Fine details and intricate geometries are maintained without compromising surface quality.
- Functional Accuracy: Smooth surfaces enhance the functionality, especially in mechanical and aerodynamic testing.
- Aesthetic Appeal: The visual quality of prototypes is significantly improved, offering a closer approximation to the final product. These smooth surfaces are particularly advantageous for industries that demand precision and aesthetic quality, such as aerospace and consumer electronics. Utilizing SLA ensures consistency and reliability in surface characteristics, aiding in the validation of complex designs.
Ultimately, SLA printing’s ability to produce smooth surfaces plays a pivotal role in reducing time-to-market and improving the overall quality of prototypes.
Cost-Effective Prototyping
Utilizing SLA printing significantly reduces prototyping costs by streamlining the production process and minimizing material waste.
Due to its precision, SLA printing eliminates the need for multiple iterations, thereby saving on costly resources and man-hours typically associated with traditional prototyping methods. This reduction in overheads makes it an economically viable solution for startups and established enterprises alike.
By leveraging “low-cost” and “high-quality” in SLA printing, companies can maximize their R&D budgets while accelerating product development.
Reduced Material Waste
SLA printing revolutionizes prototyping by minimizing material waste through precise deposition techniques. This precision is unparalleled when compared to traditional methods.
Traditional manufacturing methods often result in excessive material waste due to inefficiencies. These include processes such as subtractive manufacturing.
SLA printing, on the other hand, builds prototypes layer by layer, utilizing only the material required for the design. This method is inherently efficient and eco-friendly, substantially lowering the cost related to raw materials.
Fewer discarded materials mean significant cost savings over time, adding value to the entire product lifecycle. In an era where sustainability is key, companies benefit not only from reduced expenses but also from an enhanced reputation for environmental responsibility. By incorporating SLA printing, organizations can align their prototyping practices with sustainable development goals, ensuring both economic and ecological benefits.
Lower Production Costs
SLA printing significantly reduces expenses in the prototyping phase.
- Minimized Material Waste: Traditional methods often waste materials. SLA builds layer by layer, using only what’s needed.
- Reduced Labor Costs: Automated processes minimize labor, reducing overall expenditure.
- Lower Tooling Costs: With no need for complex molds or tooling, SLA eliminates associated costs.
- Faster Time-to-Market: Swift prototyping accelerates the development cycle, cutting down related costs.
Ultimately, SLA printing reduces financial risks associated with prototyping, enhancing overall project viability.
Diverse Material Options
SLA printing excels by offering an impressive array of materials, allowing for tailored prototyping that meets specific requirements. These materials include various resins such as standard, tough, flexible, and high-temperature-resistant options.
Each resin type provides unique properties ideal for a different range of prototypes. For instance, tough resins mimic the durability of ABS plastics, suitable for functional testing.
Selecting the appropriate material is crucial in ensuring that prototypes accurately represent the final product. Whether it’s achieving the elasticity of silicone, the toughness of engineering-grade polymers, or the clarity of glass-like resins, SLA printing delivers unparalleled flexibility.
This flexibility means companies can innovate not only in the design and function of their prototypes but also in the materials they wish to simulate. By integrating the right resin for the desired application, industries can produce highly accurate and functional prototypes, reducing development time and cost.
Versatile Applications
SLA printing’s adaptability supports diverse applications, crucial for innovative industries, from medical tools to intricate jewelry. These applications leverage high-resolution printing, ensuring precision and detail in the final product, thus aligning with stringent industry standards and aesthetic demands.
In engineering and design, this versatility enables rapid iterations of complex geometries. This capability isn’t confined to a singular domain but extends across various fields—ranging from aerospace components to customized consumer goods. This widespread applicability underscores the transformative potential of SLA printing in modern prototyping.
TABLE OF CONTENTS
Let’s Kickstart Your Custom Manufacturing
Please send your inquiries to the above email and provide as much detailed information as possible in your inquiry, e.g. 3D CAD models, 2D engineering drawings(which should detail materials, tolerances, surface finishing requirements, etc.), artwork files, and quantities needed.